
The assembly area is fully integrated with the wiring and harness fabrication areas, the encapsulation laboratory, and the inspection area, thereby creating smoother work flows.
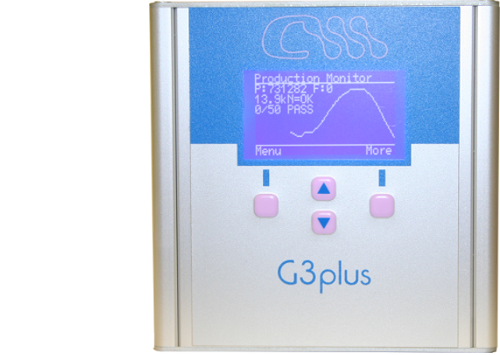
machines have been added that allow for the fabrication of multilayer PWB's. The plating and etching facilities are upgraded and fully operational, creating a well-controlled and safe environment for PWB fabrication. The relocation of the Electronic Fabrication Group to the Steven Muller Center for Advanced Technology resulted in many improvements in the fabrication of printed wiring boards (PWB's) and the assembly of components onto them. This device also could be produced by batch process and did not require any additional fabrication process. Because the area of the pressure-sensitive resistors was air-tight, the device was resistant to water.
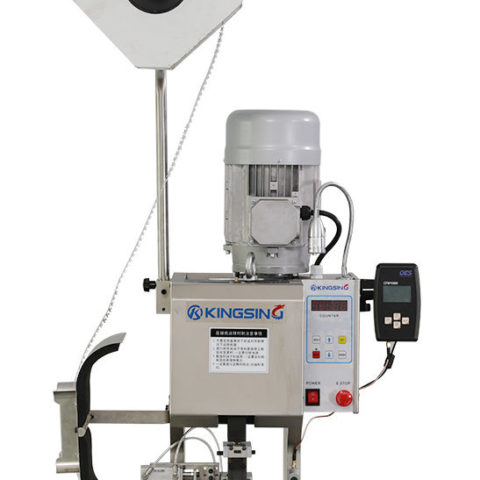
Therefore, this device could be mounted on a curved surface and have a strong resistance to external force. The sensor contained a switching circuit with diodes and was assembled on a flexible printed wiring board. Although all 64 sensors did not function, the basic characteristics and efficiency of the device were evaluated.The dimensions of each sensor were 2 mm × 2 mm. suitable.In this study, we fabricated a semiconductor tactile imager with 64 silicon piezoelectric pressure sensors on a flexible substrate. For these reasons, a semiconductor sensor is the most. To efficiently withdraw information from numerous sensors and to minimize wirings from the sensors, it is necessary to install a switching circuit on each sensor. In particular, a tactile imager with a high density of pressure sensors must be developed. To realize a robot with a high degree of functions, pressure sensors are essential. Engineers should discuss the ingredients and variables that operators need to consider before switching off a CFM. There are a lot of ingredients and if one ingredient is missing or of bad quality, you likely are not going to achieve your desired result. Crimp quality detection is similar to baking a cake. However, to create products with the highest quality and reliability, engineers, like chefs in the kitchen, need to ensure each ingredient in the process is properly prepared before sending it out to the assembly line. All CFMs come with base parameters that work for many applications.

Several variables need to be evaluated and understood for successful use of a crimp force monitor (CFM). After reference crimps are made, each subsequent crimp is compared to the reference crimp and the specified tolerance, resulting in a good or bad output. The devices use a piezoelectric sensor to detect crimping forces. Crimp force monitors allow wire harness assemblers to improve quality and boost productivity.
